www.modernitovarna.com
04
'19
Written on Modified on
Spokojenost zákazníků se odvíjí od spolehlivosti obráběcích procesů
Při plánování a zavádění obráběcích procesů se výrobci často zaměřují na řešení všech možných záležitostí svého vlastního provozu, a přitom jim uniká základní smysl jejich práce: zajištění spokojenosti zákazníků.
Spokojenost zákazníků je do značné míry určena co nejkratším časem mezi podáním objednávky a obdržením hotového produktu. V minulosti se nejkratší dodací lhůta zajišťovala výrobou tisíců identických dílů a vytvářením obrovských zásob, ze kterých bylo možno produkty okamžitě expedovat. Tento scénář hromadné výroby velkého objemu produktů s nízkou variabilitou výrobcům umožňoval včasné plnění požadavků zákazníků za postupného vývoje obráběcího procesu, a to i v případě nepředvídaných chyb a přerušení výroby.
Požadavky současného trhu jsou ovšem naprosto odlišné. Zákazníci ve stále větší míře objednávají malé dávky produktů, upravených podle jejich specifických požadavků. Výsledkem jsou velmi krátké výrobní časy jednotlivých dávek. Série totožných součástí již nejsou vyráběny po tisících, ale spíše po stovkách, desítkách nebo i jednotkách kusů. Zakázková výroba nízkého objemu produktů s vysokou variabilitou nedává žádný prostor průběžnému vývoji procesů nebo nepředvídaným přerušením výroby. Výrobci jsou pod neustálým tlakem, aby připravovali obráběcí procesy tak, že budou naprosto spolehlivé už od prvního dílu. Rozhodující je okamžitý start, vysoká rychlost, opakovatelnost a předvídatelnost.
Mnoho provozů se i přesto dále soustřeďuje na takovou „efektivitu“, kdy jsou obráběcí procesy podřizovány téměř výhradně maximální výkonnosti a minimálním nákladům. Neúmyslně se při tom přehlíží nevyhnutelná skutečnost, že prioritou je spokojenost zákazníků - obzvláště jejich požadavky na včasné dodávky.
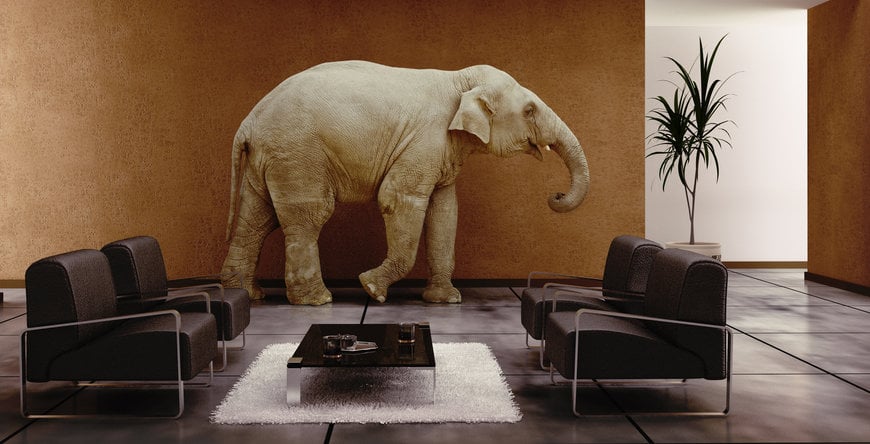
Obrázek 1:
HQ_IMG_The_Elephant_In_The_Room.jpg
QRM
Koncept nazývaný Quick Response Manufacturing (QRM) má kořeny již v počátcích éry zakázkové výroby a podtrhuje zásadní roli času ve výrobním procesu. Strategie QRM představuje, spolu se snahami o nulové ztráty a optimalizaci procesů, rámcový postup, jehož prostřednictvím lze dosahovat co nejkratších dodacích termínů a zajišťovat tak maximální spokojenost zákazníků.
Profesor Rajan Suri, který vyučoval průmyslové inženýrství na Wisconsinské univerzitě v Madisonu v 90. letech minulého století, dobře rozpoznal blížící se změny na výrobních trzích, konkrétně trendy směřující k zakázkové výrobě. V roce 1993 založil iniciativu Center for Quick Response Manufacturing. Jejím účelem je navazování strategického partnerství mezi univerzitou a výrobními společnostmi ve věci vývoje a implementace způsobů zkracování dodacích termínů. Strategie QRM jsou často uplatňovány společně s procesy štíhlé výroby, Six Sigma a podobnými přístupy ke zdokonalování procesů.
Tradiční přístup
Výrobní ředitelé tradičních obráběcích provozů se zaměřují především na maximální využití strojů. Je-li stroj nečinný, není efektivní a stojí peníze – místo aby je vydělával. Cílem je výroba velkých dávek na sklad. Díly na skladě pak vyrovnávají kolísající poptávku zákazníků.
Při zakázkové výrobě ovšem produkty nekončí na skladě, ale slouží přímo k plnění objednávek menších počtů specifických dílů. Žádné vyrovnávací skladové zásoby v tomto případě neexistují.
Situaci dále komplikují takové faktory, jako přednostní zakázky, které přicházejí neočekávaně v reakci na nouzové situace nebo speciální požadavky důležitých zákazníků. Pokud všechny stroje běží, ostatní zakázky se ve prospěch přednostních zakázek zpožďují. Z opožděných zakázek se však poté také stanou přednostní, prodlouží se dodací lhůty a ve výrobním procesu začne vznikat chaos.
Dalším problémem je, že pracovníci ve výrobě mají tendenci soustřeďovat se na hledání způsobů, jak plnit interní cíle, jako například 100% úspěšnost včasných dodávek. Plánování je pak často podřizováno tomu, jak těchto cílů dosáhnout. Zaměstnanci ve výrobě mohou například vědět, že provedení určité zakázky trvá jeden den, ale vyhradí si na ni dva dny, aby měli prostor na případné přerušení z důvodu přednostních zakázek či dalších možných prodlev.
Plánovači také přidávají časovou rezervu, aby se vyhnuli výtkám od vedení firmy. Pokud je ovšem takové chování ve výrobě obvyklé, může se dvoutýdenní dodací lhůta protáhnout klidně až na sedm týdnů. Úspěšnost včasných dodávek je dle interního měření 98 procent, pracovníci ve výrobě jsou spokojení, že své interní cíle splnili, ale zákazník, který potřebuje produkt za dva týdny, není spokojený vůbec.
Tradiční výrobní prostředí má určitá systémová omezení (viz obrázek 2). Na obrázku vlevo je dálnice s minimálním provozem, která symbolizuje nedostatečné využití zdrojů a v rámci aplikace tohoto příměru na výrobu také vysoké výrobní náklady na dokončený obrobek. Přetížená dálnice vpravo, se stojícími vozidly, představuje chaos a delší dodací lhůty, ke kterým dochází při chybách nebo když neočekávané zakázky soupeří o místo na výrobní lince. Prostřední obrázek ilustruje vyvážený a hospodárný přístup k produktivitě a využití zdrojů.
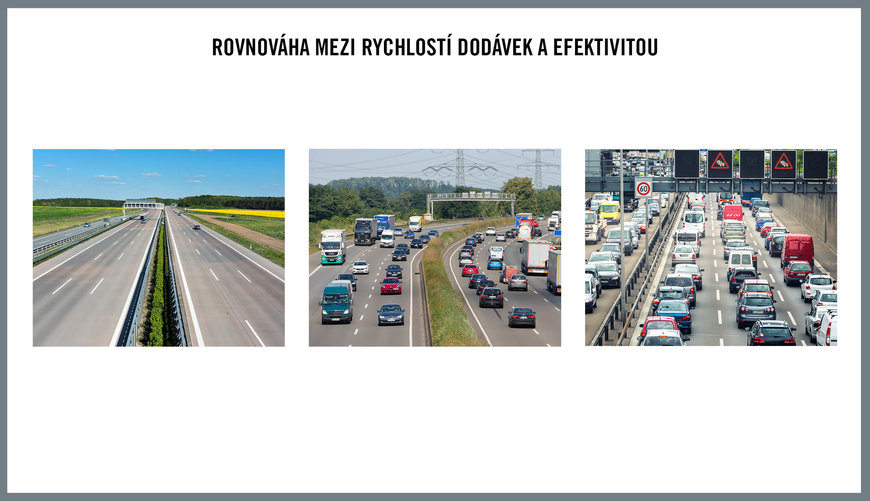
Obrázek 2:
HQ_ILL_Balance_Between_Speed_Of_Delivery_And_Efficiency.jpg
Rámcový harmonogram zakázkové výroby
V prostředí rozmanité výroby malých objemů je klíčem plná výtěžnost a konzistentní kvalita již při výrobě prvního dílu. Cílem je dodávka zakázkových produktů, kdy jediný díl jednokusové dávky stojí stejně, jako jeden díl v dávce milionu kusů, a současné zajištění okamžitého dodání.
Výroba kvalitních dílů již od samého počátku závisí na zavedení bezproblémového a spolehlivého obráběcího procesu. V současné době je moderní poukazovat na nejnovější výrobní techniky a digitalizační technologie jako na řešení problémů při obrábění. Nicméně rychlost, opakovatelnost a flexibilita vždy byly, a stále jsou, založené na provozní dokonalosti a na informovaném výrobním personálu s pozitivním myšlením a motivací. (Viz postranní panel.)
Před samotnou diskuzí o digitalizaci a optimalizaci je nezbytné podívat se na veškeré operace výrobního procesu jako na jeden celek, určit, kde dochází k plýtvání časem a zdroji, a vyvinout metody, jak toto plýtvání minimalizovat. Poté je možné začít se soustřeďovat na kvalitu nebo spolehlivost procesů.
Výrobní provoz s nulovými ztrátami
Zkracování dodacích termínů vyžaduje snižování ztrát ve výrobním procesu. Proces s nulovými ztrátami neprodukuje nadbytečné díly, plně využívá zpracovávaný materiál a eliminuje zbytečné přesuny rozpracovaných obrobků. V samotném obráběcím procesu patří mezi nehospodárné a časově náročné činnosti odstraňování otřepů, špatné jakosti povrchů, dlouhých třísek, vibrací a chyb obrábění, které vedou k výrobě neshodných dílů. Zmetky pak musí být přepracovány nebo zcela vyřazeny a vyrobeny znovu – a to vše výrobní proces prodlužuje o další čekací doby.
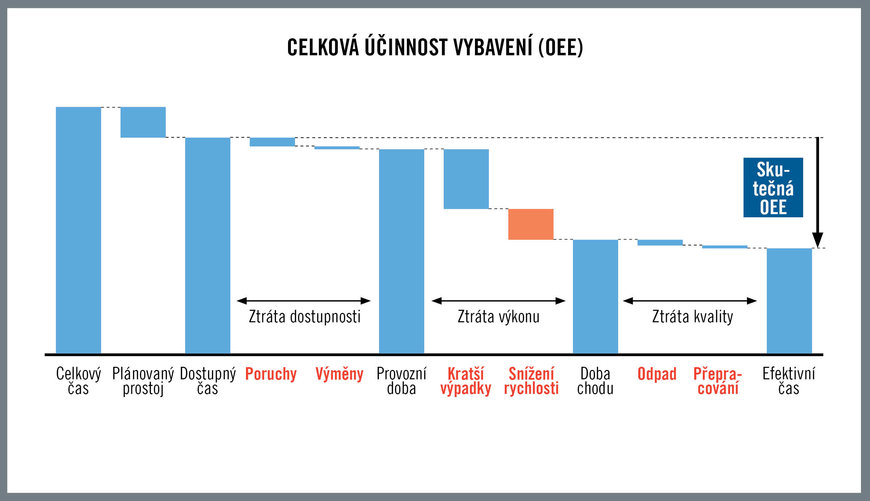
Obrázek 3:
HQ_ILL_Overall_Equipment_Efficiency_OEE.jpg
K plýtvání časem a penězi dochází i při výrobě dílů, jejichž kvalita překračuje požadavky zákazníků. Výrobní provozy si musí uvědomit, že je třeba pracovat v úrovni nejnižší možné kvality obrobku, která přesně odpovídá specifikacím a funkčním požadavkům zákazníků.
Pokud je tolerance rozměru dílu 5 mikronů, je dosahování 3 mikronů nehospodárné. K dosažení přesnější tolerance budou potřeba kvalitnější nástroje a přesnější obráběcí procesy - zákazník však za tuto nepožadovanou kvalitu nezaplatí a výrobce bude na zakázce tratit.
Respektování limitů
Při vytváření vyváženého obráběcího procesu je první fází volba nástrojů s takovou únosností, která splňuje nebo překračuje mechanická, tepelná, chemická a tribologická zatížení, která v konkrétním případě obrábění nastanou.
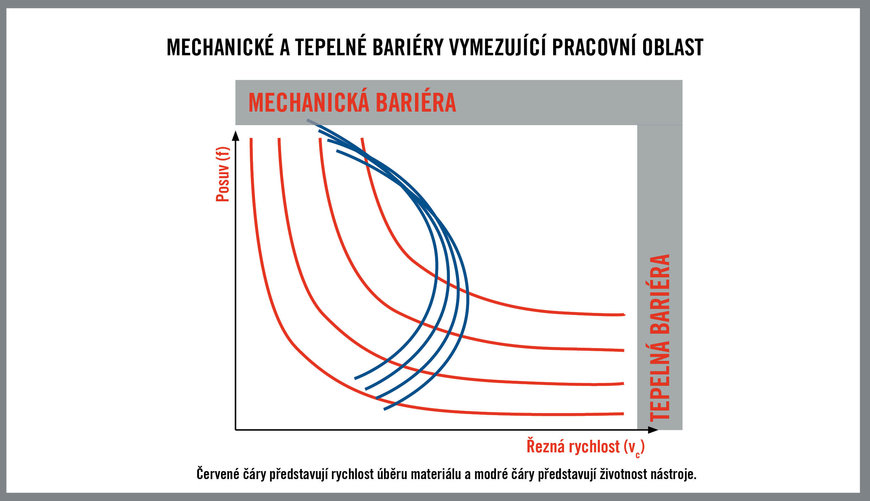
Obrázek 4:
HQ_ILL_OS_Mechanical_And_Thermal_Barriers_Frame_Working_Window.jpg
Druhá fáze pak zahrnuje volbu takových řezných podmínek, které odrážejí omezení obráběcího procesu reálnými fyzikálními faktory. Možnosti řezného nástroje jsou velmi široké, ovšem rozsah parametrů jeho efektivního využití je omezen aktuálními podmínkami ve skutečném provozu.
Možnosti nástroje se například mění v závislosti na výkonu konkrétního obráběcího stroje. Obrobitelnost zpracovávaného materiálu může omezovat řeznou rychlost nebo rychlost posuvu, a složitost či nestabilita obrobků se odrazí v náchylnosti k vibracím. Ač bude obrovské množství kombinací řezných podmínek fungovat teoreticky, omezení daná skutečnou situací výběr parametrů zajišťujících bezproblémové obrábění významně zužují.
Použití řezných podmínek mimo rámec konkrétní situace bude mít negativní dopad, včetně vyšších nákladů a nižší produktivity. Většina problémů, ke kterým při obrábění dochází, vzniká právě nerespektováním limitů, které jsou dané fyzikálními možnostmi obráběcího procesu. Pokud řezné parametry omezení v reálných podmínkách nepřekračují, je operace z technického pohledu bezpečná.
Technicky bezpečné kombinace řezných podmínek však automaticky neznamenají stejný ekonomický výsledek a změna řezných parametrů přináší i změnu nákladů na obráběcí proces. Agresivní, ale technicky bezpečné řezné podmínky sice urychlí produkci dokončených obrobků, avšak v určitou chvíli se produkce začne opět zpomalovat, neboť dochází k takovému zkrácení životnosti nástrojů, že jejich častější výměny spotřebují příliš mnoho času.
Třetí fáze dosahování vyváženého obráběcího procesu proto zahrnuje určení optimální kombinace řezných parametrů pro konkrétní situaci. Je nezbytně nutné zajistit takové pracovní podmínky, aby tyto kombinace zajistily požadovanou úroveň produktivity a hospodárnosti. Jakmile jsou zavedeny do výroby, přichází na řadu řešení běžných problémů a neustálá analýza a optimalizace výrobních procesů.
Univerzální nástroje
Zatímco vysoce výkonné specializované nástroje mohou výrobu zrychlit, rozpoznání procesních omezení může naopak podnítit volbu nástrojů vyvinutých pro univerzální použití. Jsou-li zvoleny nástroje zajišťující maximální produktivitu a hospodárnost obrábění konkrétního dílu, může přechod z jedné konfigurace obrobku na jinou vyžadovat kompletní výměnu nástrojů v zásobníku stroje. V případě zakázkové výroby, kdy se často střídají malé dávky různých dílů, může čas na takovou výměnu zcela pohltit veškerý nárůst produktivity, kterého bylo použitím nástrojů zaměřených na maximální produktivitu dosaženo.
V případech, kde se výkon nástrojů pohybuje téměř na úrovni svého maxima, mají někteří operátoři tendenci snižovat řezné parametry ve strachu ze selhání a poškození nástroje. Univerzální nástroje je možné použít, oproti nástrojům zaměřeným na produktivitu, v širším rozsahu řezných podmínek, avšak za méně agresivních parametrů. Jsou-li ke zpracování řady různých obrobků použity univerzální nástroje, může být samotné obrábění do určité míry pomalejší nebo nákladnější, ale zkrácení seřizovacích časů, eliminování zmetků a kratší dodací termíny tento rozdíl bohatě vyváží.
Závěr
Spokojenost zákazníků je cílem každého obchodního vztahu a hlavním aspektem spokojenosti zákazníků ve výrobě jsou včasné dodávky obrobených součástí. Scénáře zakázkové výroby vyvíjejí na výrobce tlak, aby optimalizovali své operace, zkrátili své dodací lhůty a zrychlili dodávky. Aplikace konceptů QRM umožňuje, spolu s iniciativami zaměřenými na nulové ztráty a optimalizaci procesů, výrobcům dosahovat rychlosti a spolehlivosti potřebné k plnění požadavků jejich zákazníků na včasné dodávky při současném zajištění ziskovosti výroby.
(Postranní panel)
Inteligentní lidé a chytré stroje
Komplexní a stále se měnící povaha zakázkové výroby je vynikající příležitostí pro implementaci nejnovější výrobní technologie, včetně interní digitalizace prostřednictvím chytrých strojů a analýzy dat, externí digitalizace v rámci integrovaného dodavatelského řetězce a webového propojení se zákazníky za účelem harmonizace dodávek a poptávky. Vlna nových technologií zdánlivě minimalizuje hodnotu lidských zásahů do výrobních operací.
Skutečnost je však opačná - stále se měnící aspekty ve scénářích zakázkové výroby důležitost lidského faktoru zvyšují. Komplikované operace vyžadují tradiční zručnost, která zahrnuje kreativitu a flexibilitu, umožňující rychlé přizpůsobování rozličným dílům, obráběným materiálům a řezným podmínkám.
Zaměstnanci ve výrobě musí mít především pozitivní myšlení a motivaci, které jsou nezbytné k tomu, aby byli schopni čelit novým a silně proměnlivým výzvám zakázkové výroby a řešit problémy s tím spojené.
K získání takového myšlení je potřeba neustálé interní vzdělávání, které zaměstnancům ve výrobě ukáže, že řešení problémů s produktivitou nemusí nezbytně znamenat obrovské výdaje a špičkové technologie. Součástí tohoto myšlení je i nutnost uvědomovat si, jak extrémně důležité je umět vyhovět požadavkům zákazníka. Poučení plynoucí ze zdokonalování nějaké konkrétní operace nebo souboru operací lze následně využít a rozšířit na podobné situace v celém výrobním provozu.
Zkušenosti z výrobního provozu lze doplňovat organizovanými vzdělávacími iniciativami, jako je program STEP (Seco Technical Education Programme), což je promyšlený a praktický program navržený k seznamování uživatelů s nejnovějšími nástrojovými systémy a technikami.
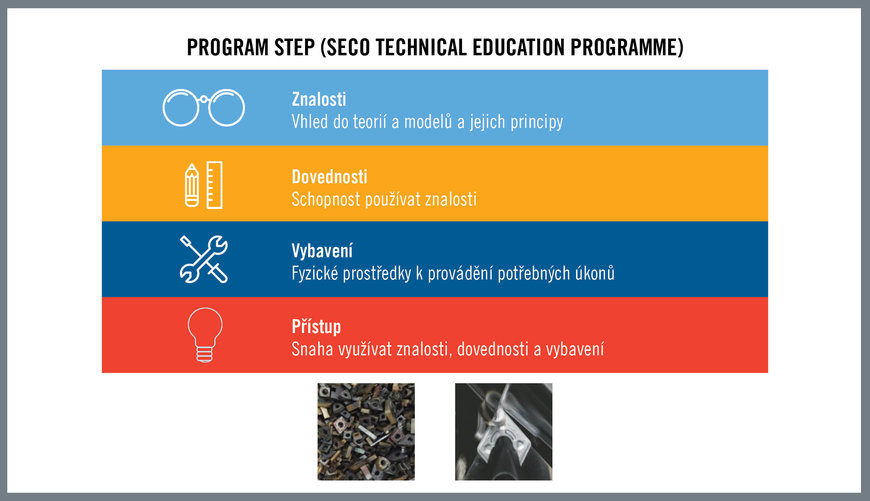
Obrázek 5:
HQ_ILL_Seco_Technical_Education_Programme.jpg
Praktické zkušenosti s analýzou a zdokonalováním procesů jsou v kombinaci s organizovanými vzdělávacími programy klíčem k zavedení kultury řešení problémů a implementace zlepšení, jejímž výsledkem bude dlouhodobý úspěch. Doplňkem takového vzdělávání jsou interaktivní informační zdroje, jako například digitální portál My Pages společnosti Seco, což je web sloužící jako podpora pro zajišťování a dodávky nástrojů, vyhledávání lepších způsobů jejich využití, optimalizaci procesů a možností technické pomoci.
V zájmu co nejlepšího využití možností situace výroby malých dávek dílů s vysokou rozmanitostí se musí management odpoutat od systémových omezení tradiční vysokoobjemové výroby. Je důležité soustředit se na posílení role zaměstnanců v rámci uvažování a kreativity, potřebných k vytvoření rovnováhy mezi produktivitou a flexibilitou, která dlouhodobě zajistí nejvyšší spokojenost zákazníků.
Autor:
Patrick de Vos, MSc, senior konzultant a manažer technických vzdělávacích programů ve společnosti Seco Tools
Požadavky současného trhu jsou ovšem naprosto odlišné. Zákazníci ve stále větší míře objednávají malé dávky produktů, upravených podle jejich specifických požadavků. Výsledkem jsou velmi krátké výrobní časy jednotlivých dávek. Série totožných součástí již nejsou vyráběny po tisících, ale spíše po stovkách, desítkách nebo i jednotkách kusů. Zakázková výroba nízkého objemu produktů s vysokou variabilitou nedává žádný prostor průběžnému vývoji procesů nebo nepředvídaným přerušením výroby. Výrobci jsou pod neustálým tlakem, aby připravovali obráběcí procesy tak, že budou naprosto spolehlivé už od prvního dílu. Rozhodující je okamžitý start, vysoká rychlost, opakovatelnost a předvídatelnost.
Mnoho provozů se i přesto dále soustřeďuje na takovou „efektivitu“, kdy jsou obráběcí procesy podřizovány téměř výhradně maximální výkonnosti a minimálním nákladům. Neúmyslně se při tom přehlíží nevyhnutelná skutečnost, že prioritou je spokojenost zákazníků - obzvláště jejich požadavky na včasné dodávky.
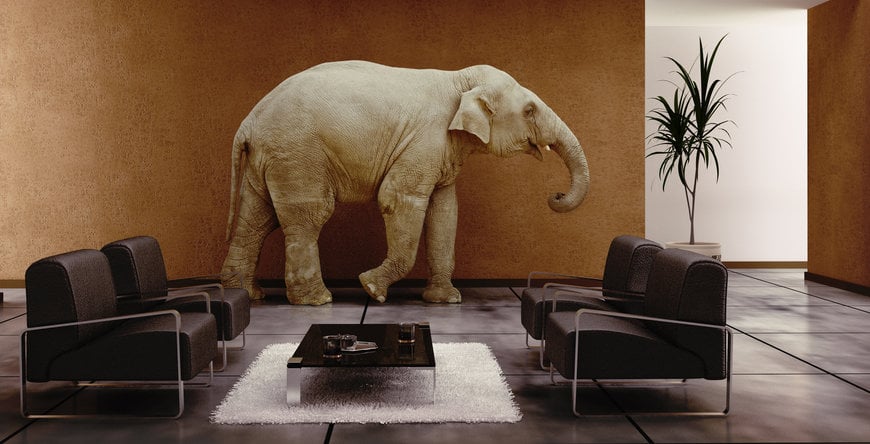
Obrázek 1:
HQ_IMG_The_Elephant_In_The_Room.jpg
QRM
Koncept nazývaný Quick Response Manufacturing (QRM) má kořeny již v počátcích éry zakázkové výroby a podtrhuje zásadní roli času ve výrobním procesu. Strategie QRM představuje, spolu se snahami o nulové ztráty a optimalizaci procesů, rámcový postup, jehož prostřednictvím lze dosahovat co nejkratších dodacích termínů a zajišťovat tak maximální spokojenost zákazníků.
Profesor Rajan Suri, který vyučoval průmyslové inženýrství na Wisconsinské univerzitě v Madisonu v 90. letech minulého století, dobře rozpoznal blížící se změny na výrobních trzích, konkrétně trendy směřující k zakázkové výrobě. V roce 1993 založil iniciativu Center for Quick Response Manufacturing. Jejím účelem je navazování strategického partnerství mezi univerzitou a výrobními společnostmi ve věci vývoje a implementace způsobů zkracování dodacích termínů. Strategie QRM jsou často uplatňovány společně s procesy štíhlé výroby, Six Sigma a podobnými přístupy ke zdokonalování procesů.
Tradiční přístup
Výrobní ředitelé tradičních obráběcích provozů se zaměřují především na maximální využití strojů. Je-li stroj nečinný, není efektivní a stojí peníze – místo aby je vydělával. Cílem je výroba velkých dávek na sklad. Díly na skladě pak vyrovnávají kolísající poptávku zákazníků.
Při zakázkové výrobě ovšem produkty nekončí na skladě, ale slouží přímo k plnění objednávek menších počtů specifických dílů. Žádné vyrovnávací skladové zásoby v tomto případě neexistují.
Situaci dále komplikují takové faktory, jako přednostní zakázky, které přicházejí neočekávaně v reakci na nouzové situace nebo speciální požadavky důležitých zákazníků. Pokud všechny stroje běží, ostatní zakázky se ve prospěch přednostních zakázek zpožďují. Z opožděných zakázek se však poté také stanou přednostní, prodlouží se dodací lhůty a ve výrobním procesu začne vznikat chaos.
Dalším problémem je, že pracovníci ve výrobě mají tendenci soustřeďovat se na hledání způsobů, jak plnit interní cíle, jako například 100% úspěšnost včasných dodávek. Plánování je pak často podřizováno tomu, jak těchto cílů dosáhnout. Zaměstnanci ve výrobě mohou například vědět, že provedení určité zakázky trvá jeden den, ale vyhradí si na ni dva dny, aby měli prostor na případné přerušení z důvodu přednostních zakázek či dalších možných prodlev.
Plánovači také přidávají časovou rezervu, aby se vyhnuli výtkám od vedení firmy. Pokud je ovšem takové chování ve výrobě obvyklé, může se dvoutýdenní dodací lhůta protáhnout klidně až na sedm týdnů. Úspěšnost včasných dodávek je dle interního měření 98 procent, pracovníci ve výrobě jsou spokojení, že své interní cíle splnili, ale zákazník, který potřebuje produkt za dva týdny, není spokojený vůbec.
Tradiční výrobní prostředí má určitá systémová omezení (viz obrázek 2). Na obrázku vlevo je dálnice s minimálním provozem, která symbolizuje nedostatečné využití zdrojů a v rámci aplikace tohoto příměru na výrobu také vysoké výrobní náklady na dokončený obrobek. Přetížená dálnice vpravo, se stojícími vozidly, představuje chaos a delší dodací lhůty, ke kterým dochází při chybách nebo když neočekávané zakázky soupeří o místo na výrobní lince. Prostřední obrázek ilustruje vyvážený a hospodárný přístup k produktivitě a využití zdrojů.
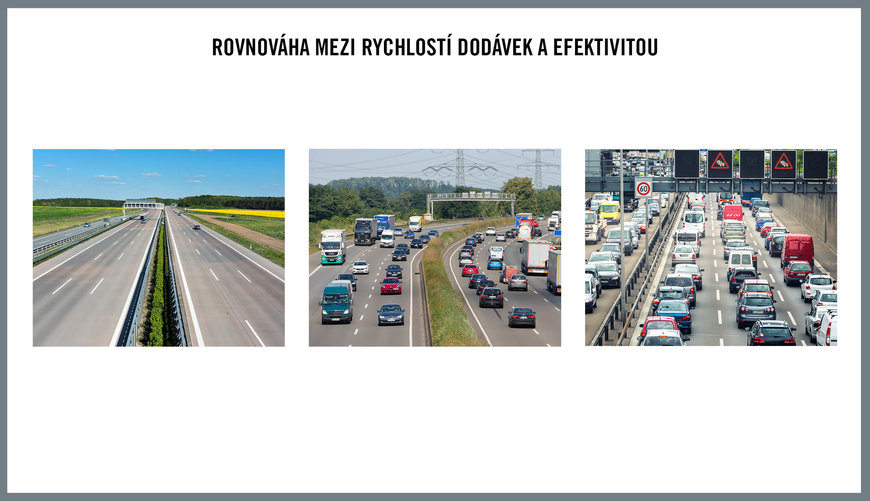
Obrázek 2:
HQ_ILL_Balance_Between_Speed_Of_Delivery_And_Efficiency.jpg
Rámcový harmonogram zakázkové výroby
V prostředí rozmanité výroby malých objemů je klíčem plná výtěžnost a konzistentní kvalita již při výrobě prvního dílu. Cílem je dodávka zakázkových produktů, kdy jediný díl jednokusové dávky stojí stejně, jako jeden díl v dávce milionu kusů, a současné zajištění okamžitého dodání.
Výroba kvalitních dílů již od samého počátku závisí na zavedení bezproblémového a spolehlivého obráběcího procesu. V současné době je moderní poukazovat na nejnovější výrobní techniky a digitalizační technologie jako na řešení problémů při obrábění. Nicméně rychlost, opakovatelnost a flexibilita vždy byly, a stále jsou, založené na provozní dokonalosti a na informovaném výrobním personálu s pozitivním myšlením a motivací. (Viz postranní panel.)
Před samotnou diskuzí o digitalizaci a optimalizaci je nezbytné podívat se na veškeré operace výrobního procesu jako na jeden celek, určit, kde dochází k plýtvání časem a zdroji, a vyvinout metody, jak toto plýtvání minimalizovat. Poté je možné začít se soustřeďovat na kvalitu nebo spolehlivost procesů.
Výrobní provoz s nulovými ztrátami
Zkracování dodacích termínů vyžaduje snižování ztrát ve výrobním procesu. Proces s nulovými ztrátami neprodukuje nadbytečné díly, plně využívá zpracovávaný materiál a eliminuje zbytečné přesuny rozpracovaných obrobků. V samotném obráběcím procesu patří mezi nehospodárné a časově náročné činnosti odstraňování otřepů, špatné jakosti povrchů, dlouhých třísek, vibrací a chyb obrábění, které vedou k výrobě neshodných dílů. Zmetky pak musí být přepracovány nebo zcela vyřazeny a vyrobeny znovu – a to vše výrobní proces prodlužuje o další čekací doby.
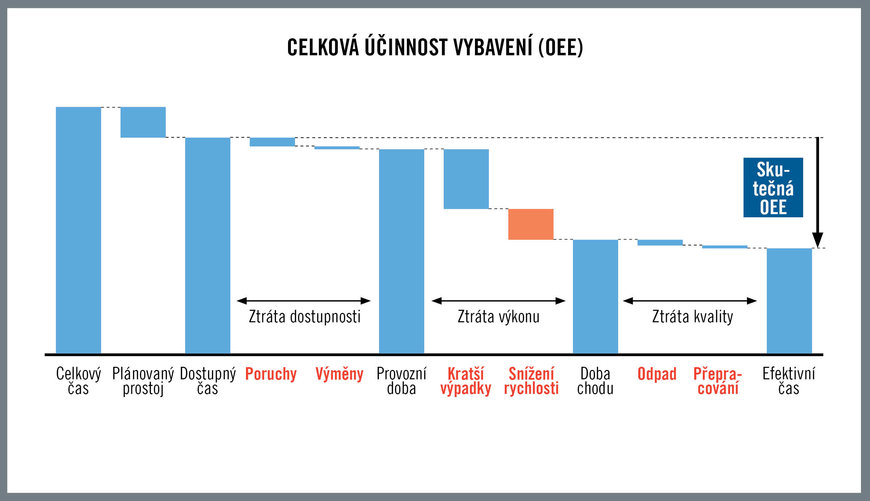
Obrázek 3:
HQ_ILL_Overall_Equipment_Efficiency_OEE.jpg
K plýtvání časem a penězi dochází i při výrobě dílů, jejichž kvalita překračuje požadavky zákazníků. Výrobní provozy si musí uvědomit, že je třeba pracovat v úrovni nejnižší možné kvality obrobku, která přesně odpovídá specifikacím a funkčním požadavkům zákazníků.
Pokud je tolerance rozměru dílu 5 mikronů, je dosahování 3 mikronů nehospodárné. K dosažení přesnější tolerance budou potřeba kvalitnější nástroje a přesnější obráběcí procesy - zákazník však za tuto nepožadovanou kvalitu nezaplatí a výrobce bude na zakázce tratit.
Respektování limitů
Při vytváření vyváženého obráběcího procesu je první fází volba nástrojů s takovou únosností, která splňuje nebo překračuje mechanická, tepelná, chemická a tribologická zatížení, která v konkrétním případě obrábění nastanou.
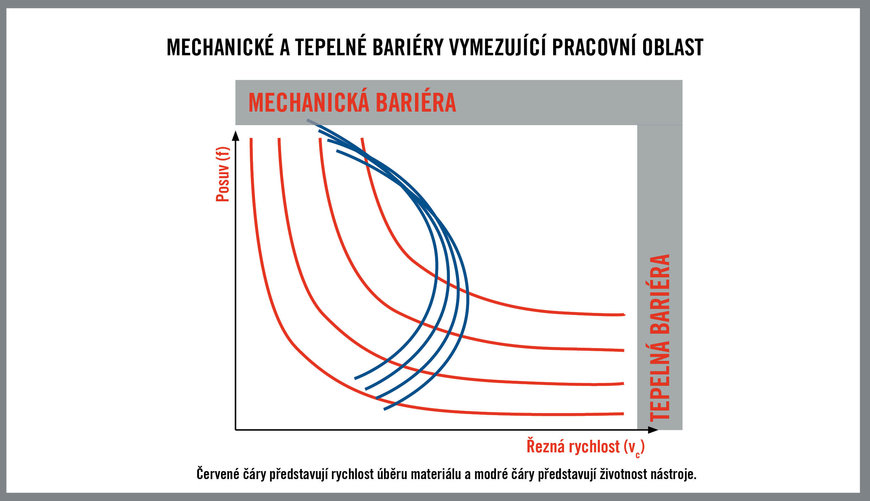
Obrázek 4:
HQ_ILL_OS_Mechanical_And_Thermal_Barriers_Frame_Working_Window.jpg
Druhá fáze pak zahrnuje volbu takových řezných podmínek, které odrážejí omezení obráběcího procesu reálnými fyzikálními faktory. Možnosti řezného nástroje jsou velmi široké, ovšem rozsah parametrů jeho efektivního využití je omezen aktuálními podmínkami ve skutečném provozu.
Možnosti nástroje se například mění v závislosti na výkonu konkrétního obráběcího stroje. Obrobitelnost zpracovávaného materiálu může omezovat řeznou rychlost nebo rychlost posuvu, a složitost či nestabilita obrobků se odrazí v náchylnosti k vibracím. Ač bude obrovské množství kombinací řezných podmínek fungovat teoreticky, omezení daná skutečnou situací výběr parametrů zajišťujících bezproblémové obrábění významně zužují.
Použití řezných podmínek mimo rámec konkrétní situace bude mít negativní dopad, včetně vyšších nákladů a nižší produktivity. Většina problémů, ke kterým při obrábění dochází, vzniká právě nerespektováním limitů, které jsou dané fyzikálními možnostmi obráběcího procesu. Pokud řezné parametry omezení v reálných podmínkách nepřekračují, je operace z technického pohledu bezpečná.
Technicky bezpečné kombinace řezných podmínek však automaticky neznamenají stejný ekonomický výsledek a změna řezných parametrů přináší i změnu nákladů na obráběcí proces. Agresivní, ale technicky bezpečné řezné podmínky sice urychlí produkci dokončených obrobků, avšak v určitou chvíli se produkce začne opět zpomalovat, neboť dochází k takovému zkrácení životnosti nástrojů, že jejich častější výměny spotřebují příliš mnoho času.
Třetí fáze dosahování vyváženého obráběcího procesu proto zahrnuje určení optimální kombinace řezných parametrů pro konkrétní situaci. Je nezbytně nutné zajistit takové pracovní podmínky, aby tyto kombinace zajistily požadovanou úroveň produktivity a hospodárnosti. Jakmile jsou zavedeny do výroby, přichází na řadu řešení běžných problémů a neustálá analýza a optimalizace výrobních procesů.
Univerzální nástroje
Zatímco vysoce výkonné specializované nástroje mohou výrobu zrychlit, rozpoznání procesních omezení může naopak podnítit volbu nástrojů vyvinutých pro univerzální použití. Jsou-li zvoleny nástroje zajišťující maximální produktivitu a hospodárnost obrábění konkrétního dílu, může přechod z jedné konfigurace obrobku na jinou vyžadovat kompletní výměnu nástrojů v zásobníku stroje. V případě zakázkové výroby, kdy se často střídají malé dávky různých dílů, může čas na takovou výměnu zcela pohltit veškerý nárůst produktivity, kterého bylo použitím nástrojů zaměřených na maximální produktivitu dosaženo.
V případech, kde se výkon nástrojů pohybuje téměř na úrovni svého maxima, mají někteří operátoři tendenci snižovat řezné parametry ve strachu ze selhání a poškození nástroje. Univerzální nástroje je možné použít, oproti nástrojům zaměřeným na produktivitu, v širším rozsahu řezných podmínek, avšak za méně agresivních parametrů. Jsou-li ke zpracování řady různých obrobků použity univerzální nástroje, může být samotné obrábění do určité míry pomalejší nebo nákladnější, ale zkrácení seřizovacích časů, eliminování zmetků a kratší dodací termíny tento rozdíl bohatě vyváží.
Závěr
Spokojenost zákazníků je cílem každého obchodního vztahu a hlavním aspektem spokojenosti zákazníků ve výrobě jsou včasné dodávky obrobených součástí. Scénáře zakázkové výroby vyvíjejí na výrobce tlak, aby optimalizovali své operace, zkrátili své dodací lhůty a zrychlili dodávky. Aplikace konceptů QRM umožňuje, spolu s iniciativami zaměřenými na nulové ztráty a optimalizaci procesů, výrobcům dosahovat rychlosti a spolehlivosti potřebné k plnění požadavků jejich zákazníků na včasné dodávky při současném zajištění ziskovosti výroby.
(Postranní panel)
Inteligentní lidé a chytré stroje
Komplexní a stále se měnící povaha zakázkové výroby je vynikající příležitostí pro implementaci nejnovější výrobní technologie, včetně interní digitalizace prostřednictvím chytrých strojů a analýzy dat, externí digitalizace v rámci integrovaného dodavatelského řetězce a webového propojení se zákazníky za účelem harmonizace dodávek a poptávky. Vlna nových technologií zdánlivě minimalizuje hodnotu lidských zásahů do výrobních operací.
Skutečnost je však opačná - stále se měnící aspekty ve scénářích zakázkové výroby důležitost lidského faktoru zvyšují. Komplikované operace vyžadují tradiční zručnost, která zahrnuje kreativitu a flexibilitu, umožňující rychlé přizpůsobování rozličným dílům, obráběným materiálům a řezným podmínkám.
Zaměstnanci ve výrobě musí mít především pozitivní myšlení a motivaci, které jsou nezbytné k tomu, aby byli schopni čelit novým a silně proměnlivým výzvám zakázkové výroby a řešit problémy s tím spojené.
K získání takového myšlení je potřeba neustálé interní vzdělávání, které zaměstnancům ve výrobě ukáže, že řešení problémů s produktivitou nemusí nezbytně znamenat obrovské výdaje a špičkové technologie. Součástí tohoto myšlení je i nutnost uvědomovat si, jak extrémně důležité je umět vyhovět požadavkům zákazníka. Poučení plynoucí ze zdokonalování nějaké konkrétní operace nebo souboru operací lze následně využít a rozšířit na podobné situace v celém výrobním provozu.
Zkušenosti z výrobního provozu lze doplňovat organizovanými vzdělávacími iniciativami, jako je program STEP (Seco Technical Education Programme), což je promyšlený a praktický program navržený k seznamování uživatelů s nejnovějšími nástrojovými systémy a technikami.
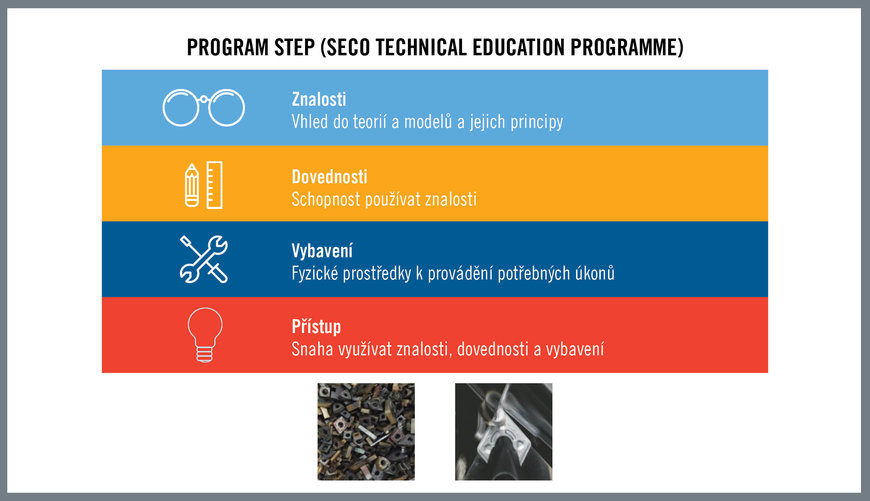
Obrázek 5:
HQ_ILL_Seco_Technical_Education_Programme.jpg
Praktické zkušenosti s analýzou a zdokonalováním procesů jsou v kombinaci s organizovanými vzdělávacími programy klíčem k zavedení kultury řešení problémů a implementace zlepšení, jejímž výsledkem bude dlouhodobý úspěch. Doplňkem takového vzdělávání jsou interaktivní informační zdroje, jako například digitální portál My Pages společnosti Seco, což je web sloužící jako podpora pro zajišťování a dodávky nástrojů, vyhledávání lepších způsobů jejich využití, optimalizaci procesů a možností technické pomoci.
V zájmu co nejlepšího využití možností situace výroby malých dávek dílů s vysokou rozmanitostí se musí management odpoutat od systémových omezení tradiční vysokoobjemové výroby. Je důležité soustředit se na posílení role zaměstnanců v rámci uvažování a kreativity, potřebných k vytvoření rovnováhy mezi produktivitou a flexibilitou, která dlouhodobě zajistí nejvyšší spokojenost zákazníků.
Autor:
Patrick de Vos, MSc, senior konzultant a manažer technických vzdělávacích programů ve společnosti Seco Tools